How 3D Modeling Enhances Mechanical Part Design
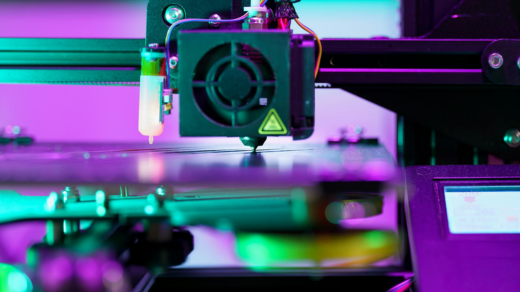
In the world of modern engineering and manufacturing, 3D design and modeling have become essential tools for developing high-precision mechanical parts. The ability to create, visualize, and refine designs in a virtual environment has revolutionized industries such as aerospace, automotive, medical, and industrial manufacturing. By leveraging 3D modeling technology, engineers and designers can achieve greater accuracy, efficiency, and innovation in mechanical part design.
But how exactly does 3D design and modeling enhance the process of creating mechanical parts? Let’s explore the key benefits, real-world applications, and technological advancements that make 3D modeling an indispensable asset in modern engineering.
1. Improved Design Accuracy and Precision
One of the most significant advantages of 3D design and modeling is the ability to create highly accurate and precise mechanical parts. Traditional 2D drawings can sometimes lead to misinterpretations or errors in measurements, whereas 3D models provide a detailed and exact representation of a component.
With advanced CAD (Computer-Aided Design) software, engineers can fine-tune dimensions, material specifications, and structural integrity to ensure optimal functionality. This level of precision minimizes the chances of design flaws, reducing the need for costly modifications later in the manufacturing process.
2. Faster Prototyping and Iteration
Before the advent of 3D modeling, designing mechanical parts involved lengthy manual drafting and multiple physical prototypes. Today, 3D modeling accelerates this process by allowing engineers to create digital prototypes that can be tested, modified, and optimized before production begins.
By using simulation and stress analysis tools within CAD software, engineers can quickly identify weaknesses or inefficiencies in a design and make necessary adjustments in real time. This iterative approach drastically reduces development time and costs while ensuring that the final product meets all functional and performance requirements.
3. Enhanced Visualization and Communication
One of the biggest challenges in mechanical design is ensuring that all stakeholders—engineers, manufacturers, clients, and suppliers—are on the same page. 3D design and modeling improve communication by providing a clear, visual representation of a part, making it easier to understand its structure, function, and assembly process.
Instead of relying on complex 2D schematics, engineers can present interactive 3D models that allow stakeholders to explore a part from different angles, zoom in on intricate details, and even test virtual assembly processes. This visual clarity helps eliminate misunderstandings and speeds up decision-making.
4. Optimized Material Usage and Sustainability
In mechanical part design, material selection plays a crucial role in determining performance, cost, and environmental impact. 3D modeling allows engineers to experiment with different materials and evaluate their effects on the final product without the need for physical trials.
By simulating how a part will behave under real-world conditions, designers can optimize material usage, reducing waste and improving sustainability. This is particularly important in industries such as aerospace and automotive, where lightweight and high-strength materials are essential for fuel efficiency and durability.
5. Seamless Integration with Advanced Manufacturing Techniques
As manufacturing technologies such as CNC machining, 3D printing, and laser cutting continue to evolve, 3D design and modeling play a vital role in bridging the gap between design and production. Digital 3D models can be directly exported to manufacturing machines, ensuring seamless and error-free fabrication.
For example, in additive manufacturing (3D printing), a 3D model is sliced into layers and used as a blueprint for printing the part with extreme precision. Similarly, in CNC machining, 3D models guide cutting tools to shape raw materials with accuracy down to microns. This direct integration streamlines the transition from design to production, reducing errors and enhancing efficiency.
6. Cost Reduction and Increased Efficiency
The ability to detect and fix design flaws early in the process leads to significant cost savings. Traditional methods of manufacturing often involve multiple rounds of prototyping, which can be expensive and time-consuming. 3D design and modeling eliminate much of this trial-and-error process by allowing engineers to identify and address potential issues digitally.
Additionally, 3D models can be used for virtual assembly simulations, ensuring that parts fit together perfectly before actual production begins. This prevents costly errors and material waste, ultimately leading to a more efficient and cost-effective manufacturing process.
7. Greater Flexibility in Design Customization
With 3D design and modeling, customization becomes easier and more accessible. Engineers can quickly modify existing designs to create custom parts tailored to specific requirements. Whether it’s adapting a component to fit a unique application or improving performance characteristics, the flexibility offered by 3D modeling allows for innovation without significant delays.
Industries such as medical device manufacturing and aerospace heavily rely on this capability, as many components must be tailored to precise specifications to meet regulatory and performance standards.
8. Advanced Simulation and Testing
One of the most powerful features of modern 3D design and modeling software is the ability to perform advanced simulations before physical production. Engineers can test mechanical parts under simulated real-world conditions to analyze factors such as:
- Stress and load distribution
- Thermal expansion and heat resistance
- Fluid dynamics and aerodynamics
These simulations provide valuable insights into how a part will perform in actual use, allowing for preemptive modifications to enhance strength, efficiency, and reliability. This predictive analysis minimizes failures and ensures that the final product is both durable and high-performing.
9. Simplified Manufacturing Documentation and Compliance
Manufacturing industries require detailed documentation and compliance with industry standards. 3D design and modeling simplify this process by generating accurate and comprehensive technical drawings, assembly guides, and part specifications.
Many CAD software solutions also include built-in compliance checks that ensure designs meet industry regulations such as ISO, ASME, or ASTM standards. This automation reduces the risk of non-compliance and streamlines the approval process for production.
10. Supporting Industry 4.0 and Smart Manufacturing
As industries move toward Industry 4.0, integrating 3D design and modeling with smart manufacturing processes is becoming increasingly important. Digital twin technology, for instance, creates a virtual replica of a physical component that can be monitored in real time for performance tracking and predictive maintenance.
Additionally, cloud-based 3D modeling enables collaborative design workflows, allowing teams across the globe to work on the same project simultaneously. This level of digital connectivity enhances efficiency, innovation, and overall productivity in modern manufacturing environments.
Conclusion: The Future of 3D Design and Modeling in Mechanical Part Development
The impact of 3D design and modeling on mechanical part development is undeniable. From improving accuracy and reducing costs to enabling advanced simulations and seamless manufacturing integration, this technology has transformed the way engineers and manufacturers approach product design.
As digital tools and manufacturing technologies continue to evolve, 3D modeling will play an even greater role in shaping the future of engineering. Whether designing a simple mechanical component or a highly complex aerospace part, leveraging 3D design and modeling ensures optimal performance, efficiency, and innovation.
To explore high-quality 3D modeling solutions tailored to your needs, visit AP3D Custom and discover how cutting-edge technology can enhance your mechanical part designs.