One Stop Pallet Racking Services: Streamlining Warehouse Operations
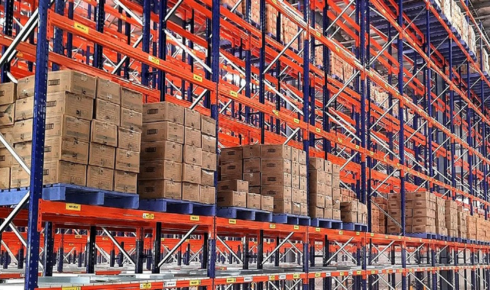
This article explores the efficiency and benefits of one-stop pallet racking services in optimizing warehouse operations. From design to installation and maintenance, such services offer a streamlined solution for businesses looking to enhance storage capacity, organization, and overall operational effectiveness within their warehouse facilities.
One Stop Pallet Racking offers comprehensive solutions for warehouse management, transforming efficiency from the ground up. Their expert services in design, installation, and maintenance ensure space optimization and operational excellence. By focusing on streamlined processes, businesses can significantly enhance storage and organization, driving both productivity and cost-effectiveness in their facilities.
Importance of Efficient Pallet Racking Systems
Efficient pallet racking systems play a crucial role in optimizing warehouse operations and maximizing storage space. By utilizing a well-designed pallet racking system, businesses can significantly increase their storage capacity, allowing for better organization and easier access to inventory. This efficiency in storage not only enhances the overall workflow within the warehouse but also improves inventory management by reducing the risk of errors and stock discrepancies. With the ability to store goods vertically, pallet racking systems make the most of the available space, which is particularly valuable in warehouses where space is limited. This optimization of storage space also leads to cost savings, as businesses can avoid the need for additional storage facilities or costly expansions. Ultimately, an efficient pallet racking system is crucial for businesses looking to streamline their warehouse operations, increase productivity, and improve overall efficiency.
Moreover, efficient pallet racking systems contribute to a safer working environment by reducing clutter and minimizing the risk of accidents. With designated storage locations for each pallet, employees can easily locate and access goods without the need to navigate through disorganized stacks of inventory. This organized approach not only enhances workplace safety but also boosts productivity by reducing the time spent searching for specific items. Additionally, efficient pallet racking systems contribute to better inventory control and tracking, as goods are stored in a systematic manner that allows for accurate stock monitoring and replenishment. By implementing an efficient pallet racking system, businesses can create a more streamlined and productive warehouse environment that benefits both employees and overall operations.
Types of Pallet Racking Solutions
There are several types of pallet racking solutions available to optimize storage efficiency in warehouses and distribution centers. One common type is selective pallet racking, which is the most popular and versatile option. It allows for direct access to each pallet, making it easy to retrieve and store items quickly. Another type is drive-in pallet racking, which maximizes storage capacity by allowing forklifts to drive directly into the racking system to load and unload pallets. This solution is ideal for storing large quantities of the same SKU and can significantly increase storage density.
In addition, there is push-back pallet racking, which operates on a last-in, first-out (LIFO) basis. This system uses carts on inclined rails to store pallets and allows for multiple pallets to be stored in each lane. This type of racking is suitable for warehouses with limited space looking to maximize storage capacity while maintaining quick access to inventory. Cantilever racking is another type that is designed for storing long and bulky items such as lumber, pipes, and furniture. It features arms that extend from the upright columns to support the items, making it easy to load and unload using forklifts or cranes.
One Stop Pallet Racking Brisbane offers a comprehensive range of storage solutions, including push-back and cantilever racking. With innovative designs tailored to maximize space, this company ensures optimal use of limited areas. Visit One Stop Pallet Racking Brisbane to explore how these systems efficiently accommodate diverse inventory needs, enhancing warehouse organization and access.
Benefits of Consolidating Pallet Racking Services
Consolidating pallet racking services offers a multitude of benefits for businesses looking to streamline their operations and maximize efficiency. By centralizing all pallet racking services with a single provider, companies can enjoy cost savings through bulk discounts and reduced administrative overhead. This consolidation allows for better negotiation power with the service provider, leading to more competitive pricing and customized solutions tailored to the specific needs of the business. Additionally, having a single point of contact for all pallet racking services simplifies communication and ensures consistent quality and service standards across all locations and projects. This streamlined approach not only saves time and resources but also fosters stronger relationships between the business and the service provider, leading to improved collaboration and better outcomes.
Furthermore, consolidating pallet racking services promotes standardization and consistency in the design, installation, and maintenance of pallet racking systems throughout the organization. By working with a single provider, businesses can ensure that best practices and industry standards are followed consistently across all facilities, reducing the risk of errors, inconsistencies, and safety hazards. This standardization also facilitates easier monitoring and tracking of inventory and assets, enhancing overall visibility and control over the supply chain. With a centralized approach to pallet racking services, businesses can achieve greater operational efficiency, improved safety standards, and enhanced productivity, ultimately leading to a more streamlined and cost-effective warehouse management system.
Maximizing Warehouse Space with Pallet Racking
Maximizing warehouse space with pallet racking is essential for efficiently utilizing the available area and optimizing storage capacity. Pallet racking systems are designed to store goods vertically, making effective use of the vertical space in a warehouse. By utilizing the height of the facility, businesses can significantly increase their storage capacity without expanding the physical footprint of the warehouse. This is achieved by stacking pallets on top of each other, supported by sturdy racking systems that ensure safety and accessibility. Moreover, pallet racking systems can be customized to fit the specific needs of the warehouse, such as adjusting shelf heights and configurations to accommodate different sizes and types of goods. This versatility allows businesses to maximize space utilization while maintaining organized inventory management practices.
Implementing pallet racking systems also enhances warehouse efficiency by facilitating easy access to stored goods. By organizing inventory vertically with pallet racking, businesses can reduce the time and effort required to locate and retrieve specific items. This streamlined process not only improves operational efficiency but also minimizes the risk of errors and damage during handling. Additionally, pallet racking systems enable better inventory visibility, making it easier for warehouse staff to monitor stock levels and manage inventory rotation effectively. With optimized space utilization and improved accessibility, businesses can enhance their overall warehouse operations, leading to increased productivity and cost savings in the long run.
Factors to Consider When Implementing Pallet Racking Systems
When implementing pallet racking systems in a warehouse or storage facility, several key factors need to be carefully considered to ensure optimal efficiency and safety. One crucial factor is the layout and design of the space. It is essential to analyze the available floor area, ceiling height, and any obstructions that may impact the installation of pallet racks. The layout should be planned in a way that maximizes storage capacity while allowing for efficient movement of goods and personnel within the facility. Additionally, factors such as aisle width, rack height, and column spacing must be taken into account to facilitate easy access to pallets and ensure safe handling of inventory.
Another important consideration is the type of products being stored and their individual characteristics. Factors such as weight, size, shape, and fragility of the goods will influence the choice of pallet racking system. For example, heavy-duty pallet racks with high load capacities may be required for storing bulky items, while specialized racks such as cantilever racks may be more suitable for long or irregularly shaped products. Understanding the specific requirements of the stored goods will help in selecting the most appropriate racking system that can safely accommodate the inventory without compromising the structural integrity of the racks. By carefully considering these factors, businesses can implement pallet racking systems that are tailored to their unique needs and operational requirements.
Enhancing Safety Measures in Pallet Racking Operations
Enhancing safety measures in pallet racking operations is crucial to prevent accidents and ensure a safe working environment in warehouses and distribution centers. One effective way to improve safety is through regular inspections and maintenance of pallet racking systems. Inspections should be conducted by trained personnel to identify any damage, wear and tear, or structural weaknesses in the racking components. Regular maintenance, such as repairing damaged rack components, replacing missing or broken safety pins, and ensuring proper load distribution, can help prevent accidents caused by structural failures. Implementing a schedule for routine inspections and maintenance not only enhances safety but also prolongs the lifespan of the pallet racking system, reducing the risk of costly repairs or replacements in the long run.
Another important aspect of enhancing safety in pallet racking operations is providing comprehensive training to warehouse staff. Proper training can educate employees on safe loading and unloading procedures, weight capacity limits, proper use of forklifts and other equipment, and emergency protocols in case of accidents. Training programs should be regularly updated to incorporate any changes in safety regulations or industry best practices. Investing in training not only reduces the risk of accidents but also boosts efficiency and productivity by ensuring that employees are equipped with the knowledge and skills to perform their tasks safely and effectively. By prioritizing regular inspections, maintenance, and training, businesses can create a culture of safety in pallet racking operations, protecting both employees and valuable inventory.
Customization Options for Tailored Pallet Racking Solutions
Customization options for tailored pallet racking solutions offer businesses the flexibility to design a storage system that perfectly suits their unique needs and space constraints. One key aspect of customization is the ability to choose the height, width, and depth of the racking units to maximize the use of vertical space and accommodate different pallet sizes. Adjustable beam levels provide further customization by allowing users to configure the racking to store various types of goods, from small boxes to oversized items. Additionally, customization options often include different types of decking, such as wire mesh or particle board, to cater to specific load requirements or to prevent smaller items from falling through.
Furthermore, businesses can enhance the functionality of their tailored pallet racking solutions by incorporating additional features such as dividers, labels, and signage. Dividers help to organize inventory and prevent items from shifting or falling during storage and retrieval processes. Labels and signage can improve inventory management and picking efficiency by clearly marking different zones, aisles, or specific product locations. Moreover, accessories like safety bars, backstops, and column protectors can be added to enhance the safety and durability of the racking system, ensuring a secure environment for both employees and stored goods. Overall, customization options empower businesses to create a pallet racking solution that optimizes storage capacity, improves workflow efficiency, and enhances safety in the warehouse environment.
Cost-Effective Strategies for Pallet Racking Services
Cost-effective strategies for pallet racking services involve optimizing the layout and design of the racking system to maximize storage capacity and efficiency. By conducting a thorough assessment of the warehouse space and inventory requirements, businesses can determine the most suitable racking configuration that minimizes wasted space and allows for easy access to products. Utilizing adjustable pallet racking systems can also provide flexibility to adapt to changing inventory needs without the need for costly reconfigurations. Additionally, investing in durable and high-quality pallet racking materials can reduce maintenance costs in the long run, as they are less likely to require frequent repairs or replacements.
Another cost-effective strategy for pallet racking services is implementing proper inventory management practices to ensure optimal use of the racking system. By organizing inventory based on turnover rates and implementing a first-in, first-out (FIFO) system, businesses can reduce the risk of product obsolescence and minimize the need for excessive handling of goods. Regular maintenance of the pallet racking system, including inspecting for damage and wear, can also help prevent costly accidents and downtime due to equipment failure. Furthermore, training employees on safe handling and loading practices can extend the lifespan of the racking system and reduce the risk of costly accidents or injuries.
Integrating Technology for Seamless Warehouse Management
Integrating technology for seamless warehouse management involves leveraging digital tools and solutions to optimize operations, enhance efficiency, and improve overall performance. One key aspect of this integration is the use of warehouse management systems (WMS) that provide real-time visibility into inventory levels, streamline order processing, and automate various tasks. By implementing a WMS, businesses can track goods across the supply chain, reduce errors, and improve inventory accuracy. Additionally, integrating technologies such as barcode scanners, RFID tags, and automated data capture systems can further enhance operational efficiency by enabling quick and accurate data collection, inventory tracking, and order fulfillment. These technologies help in reducing manual errors, minimizing stockouts, and enhancing overall inventory control.
Furthermore, integrating technology for seamless warehouse management also involves the use of data analytics and business intelligence tools to gain valuable insights into warehouse operations. By collecting and analyzing data related to inventory levels, order processing times, and warehouse workflows, businesses can identify trends, optimize processes, and make data-driven decisions. Predictive analytics can also be leveraged to forecast demand, optimize inventory levels, and improve resource allocation. By integrating these advanced technologies into warehouse management practices, businesses can achieve higher levels of operational efficiency, cost savings, and customer satisfaction. Ultimately, the seamless integration of technology into warehouse management can transform traditional warehouse operations into agile, data-driven processes that are responsive to changing market dynamics and customer demands.
Future Trends in Pallet Racking Innovations
Future trends in pallet racking innovations are driven by the need for increased efficiency, safety, and sustainability in warehouse operations. One key trend is the integration of automation and technology into pallet racking systems. This includes the development of smart pallet racking solutions that utilize sensors, RFID technology, and data analytics to optimize storage space utilization, inventory management, and order fulfillment processes. Automated pallet racking systems can reduce human error, increase picking accuracy, and enhance overall warehouse productivity. Additionally, advancements in robotics are enabling the development of autonomous pallet racking systems that can autonomously move and position pallets, further streamlining warehouse operations.
Another significant trend in pallet racking innovations is the focus on sustainability and eco-friendly design. As businesses increasingly prioritize environmental sustainability, pallet racking manufacturers are exploring materials and designs that minimize waste, energy consumption, and carbon footprint. This includes the use of recycled materials in pallet racking construction, as well as the development of modular and reusable racking systems that can be easily reconfigured or repurposed as warehouse needs change. Additionally, there is a growing emphasis on incorporating energy-efficient lighting and ventilation systems into pallet racking solutions to reduce power consumption and promote a greener warehouse environment. By embracing sustainable practices, future pallet racking innovations are not only enhancing operational efficiency but also contributing to a more environmentally responsible supply chain.